日立製作所(日立)は企業のデジタル変革を支える取り組みとして「Lumada」を展開しているが、自社ではどのように実践しているのだろうか。同社は2月17日、電力事業者向けのパワーグリッド機器などを手がける「日立事業所」や、社会インフラ・産業分野向けに情報制御システムなどを手がける「大みか事業所」での取り組みを報道機関向けに説明した。
直流高電圧発生装置(出典:日立)
大みか事業所はLumadaの実践工場であり、世界経済フォーラムが定める先進的な工場「Lighthouse」に日本企業で初めて選出された。Lumadaは2016年5月に提供を開始し、その特徴は顧客企業が抱えている課題の解決や、社会情勢などの観点から潜在的な課題を見つけることにある。これを実現するため日立は専門の研究開発グループを発足し、人類学や社会学などさまざまな学問を学んできた人材を取りそろえたという。
大みか事業所では、主に制御盤を製造している。制御盤は顧客企業の要望に合わせて設計するため、作業者は毎回異なる製品を組み立てることになる。その分アクシデントが発生しやすく、度々ラインに滞留が発生していたという。
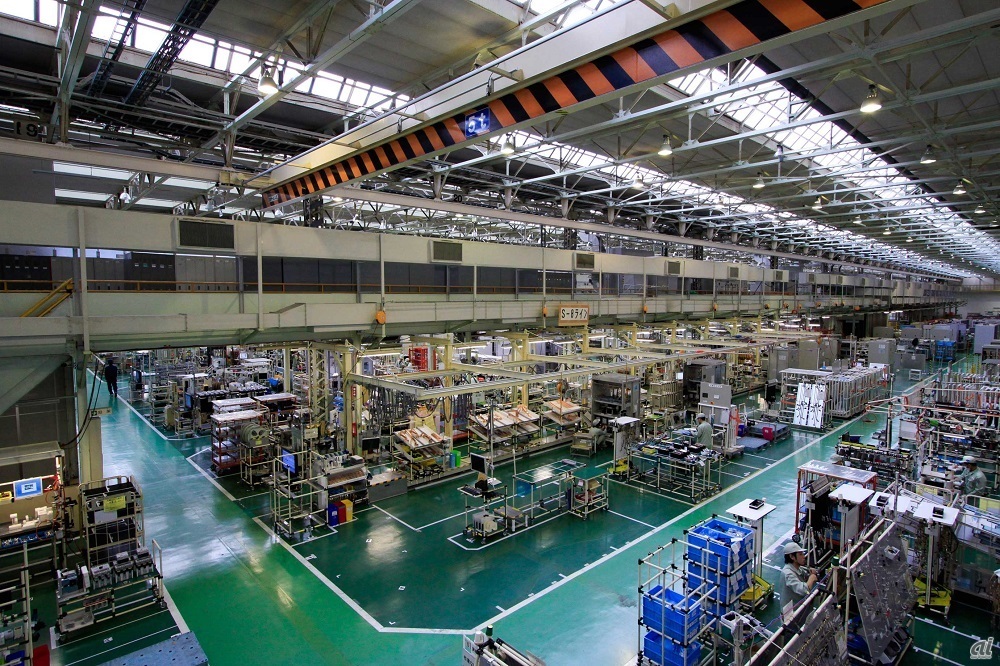
大みか事業所。作業台は「屋台」と呼ばれている(出典:日立)
こういった状況の中、日立は生産プロセスを可視化し、シミュレーションを実施。これによりラインの滞留時間を管理でき、結果として生産リードタイムを半減させることができたという。これを実現した代表的なシステムは、以下の通りだ。
進捗・稼働監視システム
RFIDタグを内蔵したカードを使って、「誰が、いつ、どこで、何の作業をしていたか」を可視化する。作業者は毎朝上司からカードを渡され、それをカードリーダーで読み取ると、やるべき作業が作業台に設置されたディスプレイの画面に表示される仕組みだ。作業の進捗状況が日次で分かることにより、責任者は「この工程が遅れそうだから、人員配置を変えよう」といった具合に、リスクの認識や対策の立案が可能となる。他のメリットについて、担当者は「われわれは顧客企業の要望に合わせて、毎回異なる製品を作る『一品ものづくり』をしている。だが、このカードにより各作業にかかる平均時間が分かるので、初めて作る製品でも組み立てにかかる時間をある程度予測することができる」と説明した。
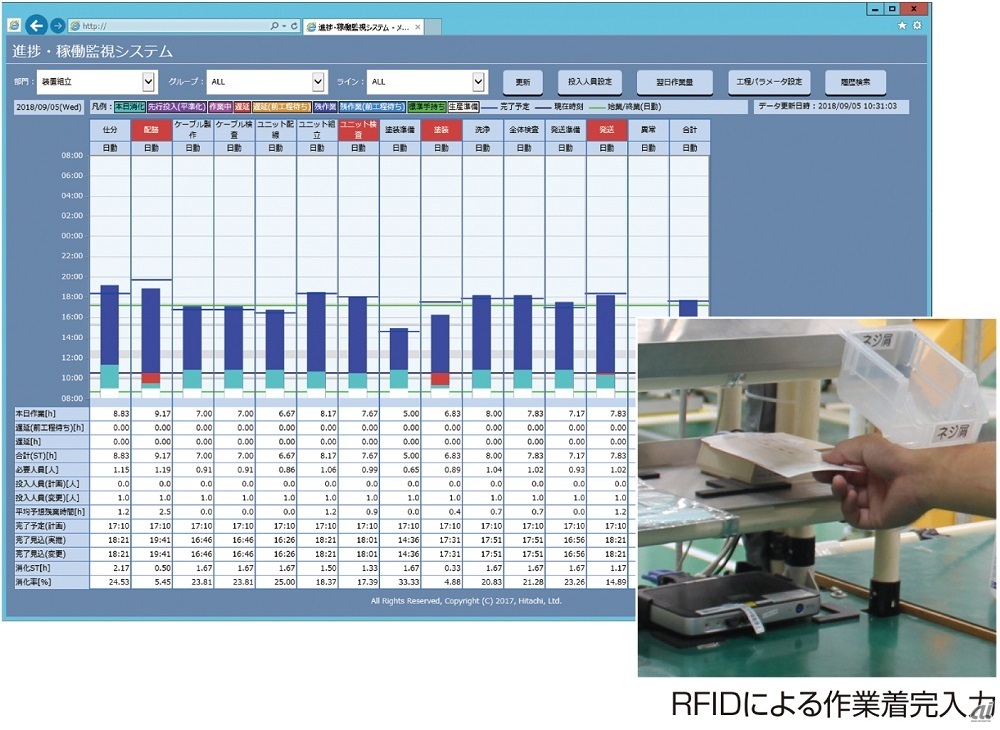
進捗・稼働監視システム(出典:日立)
分析用カメラ付き作業台車
台車に設置されたカメラが従業員の作業を終始撮影している。全ての作業工程にかかった時間を計っているので、想定より時間がかかった場合、その理由を後で分析することができる。理由を基に作業を改善することで、さらなる効率化につながるという。
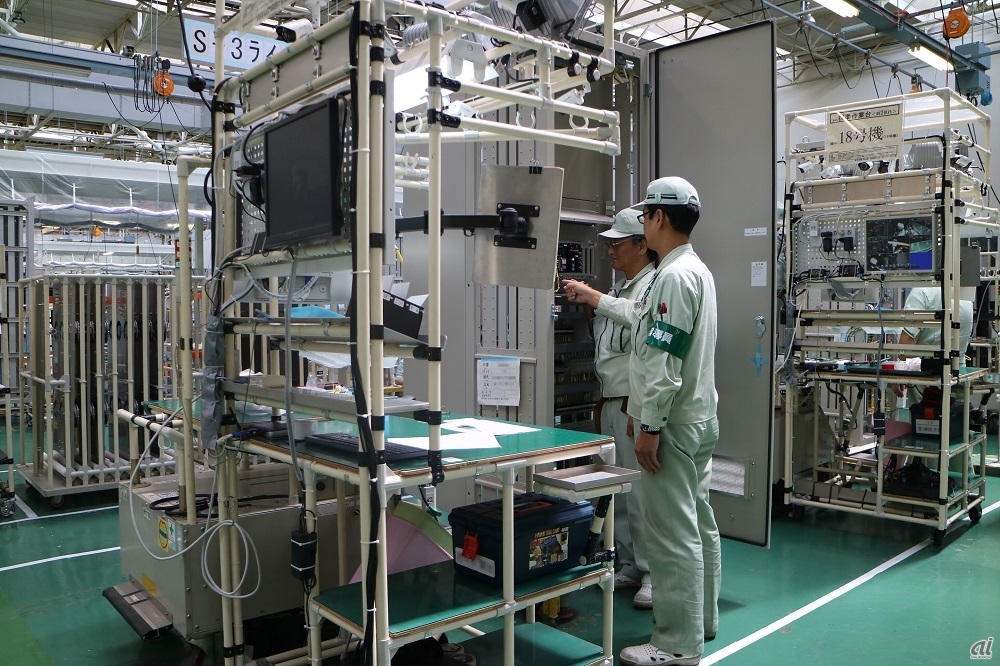
分析用カメラ付き作業台車(出典:日立)
作業改善支援システム
標準より時間がかかった作業を表にしている。作業指示図と映像を確認することで、時間がかかった理由を解明することができる。例えば配線に時間がかかった場合、作業の様子を撮影した映像を基に、普段使う工具では施工が不可能な設計だったことが判明する。
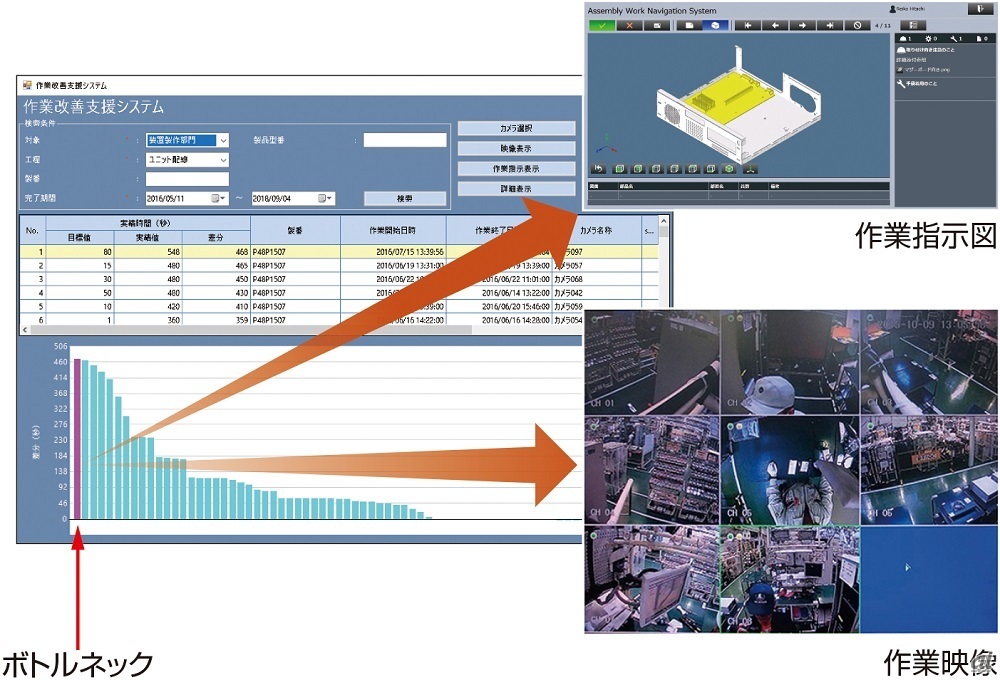
作業改善支援システム(出典:日立)
組立ナビゲーションシステム
CADデータから、製品の図面を自動的にアニメーションで作成する。元々は設計者が図面を作っていたが、一品ものづくりをしているため毎回作成する必要があった。加えて紙の資料では情報量が少ないため、経験が浅い作業者にとっては不明点が多かったという。担当者は「ベテランと新人で異なるのは、作業時間というよりも図面を読む時間だった。だが、顧客企業が作業者に望んでいるのは、図面を読むことではなく製品を作ること。そのため、システム化に踏み切った」と語った。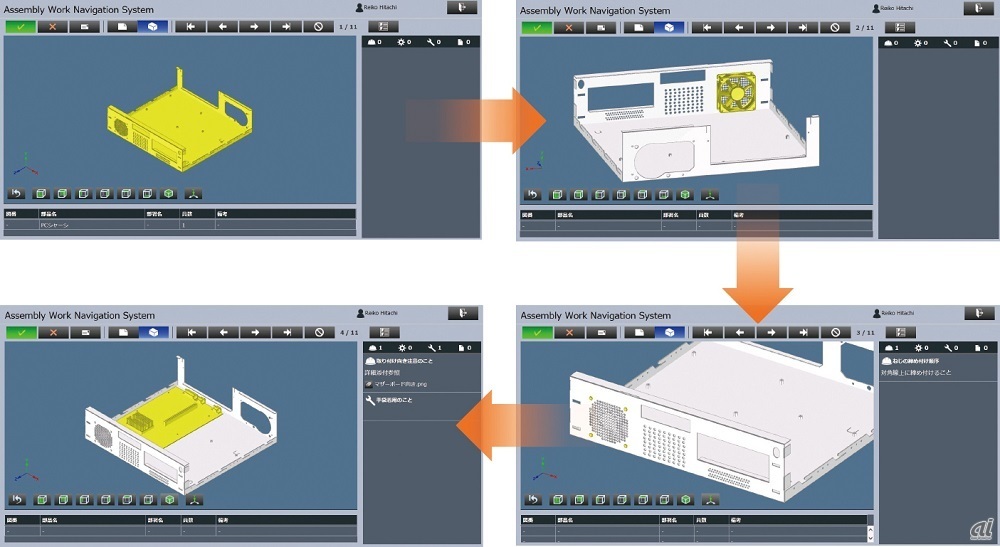
組立ナビゲーションシステム(出典:日立)
生産プロセスを可視化するシステムのほか、大みか事業所にはセキュリティの事故を意図的に起こし、それに対処する訓練をする「サイバー防衛訓練施設」もある。社会インフラへのサイバー攻撃に対処するため、人材の育成と組織の強化を目指しているという。対象は、セキュリティの専門家だけでなく企業の経営層や制御システムを運用している人々も含まれる。訓練では、リアリティーを追求するため顧客企業のシステムに近い環境を施設内に構築。日立の技術者がハッカーとして攻撃を仕掛けて、講師による支援のもと受講者がそれを防御する。世界中の最新事例を基に、さまざまな攻撃パターンを用意しているという。
サイバー防衛訓練施設(出典:日立)