梱包の際にも、自動的にダンボールを組み上げる仕組みを採用。作業者は煩雑な組立作業をしなくて済む。これは、生産拠点とダンボールの納品業者との連動で実現したもので、作業の大幅な効率化を実現している。これも、日本に拠点があるからこそ、納品業者との細かい連携を実現。その結果、成し得たものといえる。
電動ドリルは、作業後に手を離したときに発生する揺れを最低限に抑え、作業者の顔に当たったり、製品に傷を付けたりといったことがないように安全性にも配慮する工夫が凝らされている。
こうした数々の工夫から日本生産ならではの効率的な生産ラインが確立されている。
納期を短縮化
今年に入って、生産を開始したThinkPad X1 CarbonとThinkPad X250は、それぞれ生産ラインが1本ずつ設置されている。
ThinkPad X1 CarbonがT2、ThinkPad X250がT1と呼ばれるラインで生産されており、それぞれが4人で組み立てている。「基本的には、これまで米沢事業場で採用していたのと同じ仕組みを使っているが、LaVieやVersa Proに比べると作業工数が多い。そのため、作業人数が1人多くなっている」(NECパーソナルコンピュータ生産事業部グループマネージャー 須田修氏)
だが、深センの生産ラインとはまったく異なる仕組みだ。その点では、LaVieやVersa Proは、米沢の生産ラインの声を反映して、生産しやすい設計が盛り込まれているが、ThinkPadの場合には、深センでの生産ラインに最適化したものになっているともいえる。
たとえば、梱包材ひとつをとっても、誰でも組み立てられるものになっているが、LaVieのように自動的に箱が組み上がるというような工夫はされていない。かなりの枚数のシールを梱包箱に貼り付けるという作業も発生しており、これも効率的ではない。
そうしたひとつひとつの作業の差が、生産ラインに投入する人数やライン長、あるいは生産時間や品質にも影響している。
「今後、米沢事業場のThinkPadの生産ラインから上がってきた要望を設計、開発にも反映できるようにし、ThinkPadの生産性向上、品質向上につなげることでコスト削減を実現したい」(竹下氏)
ThinkPadの生産ラインでは、ハードディスクのブラケットへの固定などの前工程をインライン化しているほか、入荷した天板の外観検査の作業なども実施。さらには、配線作業には木で作られたピンセットを利用するなど、すでに独自の工夫を凝らし始めている。
キーボードのひとつひとつを打鍵して確認する作業のほか、約2時間の検査工程もこの生産ライン上で実施している。こうした独自性を持った効率的な生産手法が、米沢事業場で蓄積されればThinkPadのグローバルの生産拠点にも反映される可能性もありそうだ。
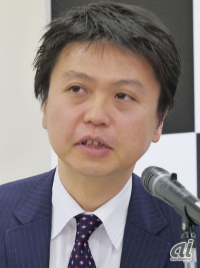
NECレノボ・ジャパングループ ダイレクト事業部長 河島良輔氏
Lappin氏は「米沢事業場で生産する強みは、納期が短縮化できる点、長年に渡り蓄積されたノウハウを活用できる点、張り巡らせた物流ルートを活用して日本のユーザーに的確に届けることができる点」と語る。NECレノボ・ジャパングループ ダイレクト事業部長の河島良輔氏は「現在、生産している製品はCTOによる受注生産であるため、リードタイムが短いことは武器になる。NECパーソナルコンピュータの工場で生産しているという安心感は大きい」とする。
現在、5営業日での納品が可能だが、「5営業日のうち受注処理に1日、2日目に部品を準備、3日目に生産ラインに投入、4日目に検査なども終了させて出荷。5日目にユーザーの手元に届くという仕組み」(竹下氏)。現在は約10日間での納期となっているが、4月の早い時期にはバッグログを解消する予定だという(生産現場はフォトレポートでも伝えている)。