NECは11月4日、モノのインターネット(IoT)の活用拡大などを含め、グループ企業の工場全体で開発生産基盤の統合を進めると発表した。
グローバル統合基幹業務システム(ERP)パッケージ「IFS Applications」を活用したサプライチェーン管理(SCM)システムや工場ごとに最適化されていた製造実行管理システム(MES)を標準化し、各工場に導入していく。またNECネットワークプロダクツの本社工場で20%の生産性向上を実現したIoT活用システムを、標準システムとして他の工場にも展開していく。

開発生産プロセス/システム標準化の概要(NEC提供)
さらにこれらのシステムを、既存の統合製品情報管理(PDM)システム「Obbligato III」や販売、調達、経理システムなどの経営システムと連携して全社統一を図る。このことで情報の一元化を実現し、工場の改善サイクル向上や継続的な商品供給など、顧客の要望に迅速で柔軟に対応できる体制を整える。
IFS Applicationsを活用したSCMシステムは、従来、NECプラットフォームズ甲府事業所に導入されていたが、同掛川事業所、白石事業所、NECプラットフォーム テクノロジーズ香港の3つの工場に導入した。また同時にNEC府中事業場の放送機器などカスタム品を扱う工場にも導入を完了した。さらに標準化されたMESは、掛川、白石の2つの工場へ導入している。
NECでは、業務プロセスとシステムの標準化により、社内リソースの有効活用、拠点間での生産調整を容易に実施できるとしている。これにより、グローバルでのQCD(クオリティ、コスト、デリバリ)の競争力強化を図る。
また、先進IoT技術を活用することで「KPI管理」「異常の見える化」「効率化、最適化」を推進する。
主要評価指標(KPI)管理では、IoTによって人、設備、モノに関する情報をリアルタイムかつ一元的に見える化ができるため、経営者、工場管理者、現場の各階層でのKPI管理の強化ができるとしている。また、ラインの異常、品質悪化の兆候などを早期に捉えられるため迅速な意思決定を可能にする。
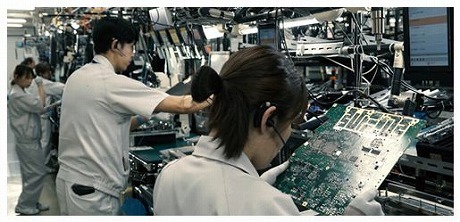
NECネットワークプロダクツ本社工場(福島県福島市)の組立検査工程(NEC提供)
NECネットワークプロダクツの本社工場では、IoT活用で、作業手順やリソースの配置を最適化し、段取り時間などの作業工数を削減できた。組立検査工程では、音声合成による作業指示と音声認識による実績入力を導入し、ハンズフリー化している。現在、NEC独自の物体指紋認証技術を活用し、プリント基板にバーコードやRFIDを貼付することなく個体を識別、生産実績や品質情報を紐づけて工程内のトレーサビリティや品質分析を行うことも進めている。