燃料ノズルという名称はあまり凄さを感じさせないが、この部品は航空機のエンジンの炎の中で、エンジン中にジェット燃料を噴射するという重要な役割を果たす。言うまでもなく、このノズルは高圧と超高温(およそ華氏3000度、摂氏1650度)に耐えられる必要がある。
「GEが再設計を試みる前は、このノズルは別々の業者から調達された20個の異なる部品から、ろう付けや溶接をして苦労して製造されていた。3Dプリンティングは、その過程を完全に変えた」と、GE Aviationの付加製造技術担当ジェネラルマネージャーGreg Morris氏は述べている。
Morris氏はGEに務める以前は、自分の会社であるMorris Technologiesを経営していた。これは米オハイオ州シンシナティにあったラピッドプロトタイピングを専門とする会社で、10年以上にわたってGEと緊密に協力しながら仕事を進めていた。同社は、数年にわたって金属焼結やコバルトとクロムからなる超合金の実験を続けていた。そして2011年、再設計に最も適した部品として、燃料ノズルに集中的に取り組み始めた。GEが2012年に同社を買収したことで、3Dプリンティングによってこの燃料ノズルを実現する機運が高まった。
その結果がこの工学上の驚異である、古いノズルが内部に持つ複雑な管やチャンバーを完全に再現した単体の部品だ。このノズルは、微細な合金の粉末をプリンタのプラットフォームに吹き付け、レーザーで過熱することによって融着させていくという作業を3000回繰り返すという工程によって作られた。新しいノズルが素晴らしいのは、いくつにもわたる製造工程を1つにまとめたことだけではない。このノズルは古いものよりも25%軽量で、しかもなんと5倍の耐久力を持つという材料科学の奇跡であり、GEとフランスのSnecma(Safran)のジョイントベンチャーCFM Internationalが開発したGEの次世代エンジン「LEAP」を積んだ航空機を導入する航空会社は、1機につき年間300万ドルのコスト削減が可能だという。
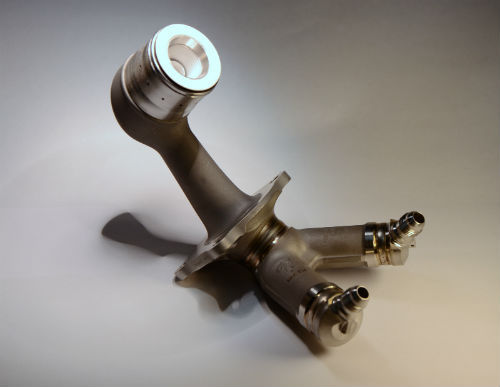
3Dプリンティングが導入される前、この燃料ノズルは20個の異なる部品から成っていた。今では部品はたった1つで、従来より25%軽量、耐久性は5倍になった。
提供:GE
「3D付加製造プロセスがなければ、これほど複雑な部品をこの水準で製造することは不可能だった」とMorris氏は述べている。
Morris氏によれば、現在までに800億ドル相当のエンジンが発注されており、3Dプリンティングで製造した燃料ノズルはエンジン1基あたり19個使われている。これらはAirbusの「A320neo」、Boeingの「737MAX」および「777X」に使われる予定だ。Morris氏とGEの前には、2020年までに10万個の燃料ノズルをプリントし、いずれは年間4万4000個まで製造能力を拡大するという課題が横たわっている。現時点での3Dプリンティング技術の水準では到達できないように思える目標だ。これは、チャカン工場のような拠点が、世界的な製造能力不足を補うために動員されることを意味している。これは、単に同社のサーバに置かれているパーツのCADの設計図を使って、ノズルをプリントアウトすれば可能だからこそできることだ。
しかし現時点では、チャカンのような製造拠点は、GE社内の重要な既存ニーズに対応するために稼働している。1つしかない複雑な機械が故障した場合、交換用の部品を見つけるのは困難で、事業に遅れと損失をもたらす。そういった部品は、多くの場合ゼロから設計し直して製造する必要がある。しかし、ハイエンドの部品を再生するには、部品を支持して位置を固定するための「治具」やその他の専用の道具から作らなくてはならない。