プロトタイプ製作チームの責任者を務めるのは、Soeren Papsdorf氏だ。Papsdorf氏が率いるチームは、まず社内の3Dプリンタを使って、さまざまな精密部品の計画やテストを始める。
ロボットが形になってくると、テスト可能なプロトタイプを製作し、ケーブルの配線などのトラブルになりやすい部分が実際にどのようになるかを調べ始める。
同氏のチームは、ケーブルトレイの配線がうまくいかないと判明するたびに部品メーカーに新しい部品を注文する代わりに、設計者に情報を渡し、すぐに設計を修正して新しい部品をプリントする。
しかも、同社が3Dプリンティングを使っているのはプロトタイプ製作だけではない。Papsdorf氏は、複雑なロボットを生産できる既成の生産ラインを、簡単に買ってくることなどできないと説明する。このためKUKAでは、3Dプリンタを使って、製造に使用する治具や固定具をすべて社内で作っているという。
これによって製造開始までの時間を短縮できると同時に、製造プロセスの修正や最適化も、短時間のダウンタイムで行うことができる。
ベースモデルの設計とテストが終わると、応用エンジニアリングチームが参加し、どうすれば顧客がそのロボットを一番活用できるかを検討する。
顧客が特定の作業を行うロボットを必要としているのなら(例えば何か壊れやすいものを持ち上げるなど)、同チームがロボットにその機能を持たせるエンドエフェクタを生み出す。
Otmar Honsberg氏が率いる同チームは最近、顧客の要望に応えて、カメラとソフトウェアを組み合わせることで、さまざまな容器から特定の物体を見つけて拾い上げることができるグリッパーを設計し、部品を3Dプリンタで製作して作ったという。
この次元のカスタマイズは、KUKAの社内にエンドエフェクタを繰り返し製作してテストできる能力がなければ不可能だ。
KUKAは1つの事例にすぎないが、その仕事ぶりは、製造業の大手企業が、設計と製造プロセスのさまざまなステージで3Dプリンティングを活用していることを伺わせるものだった。
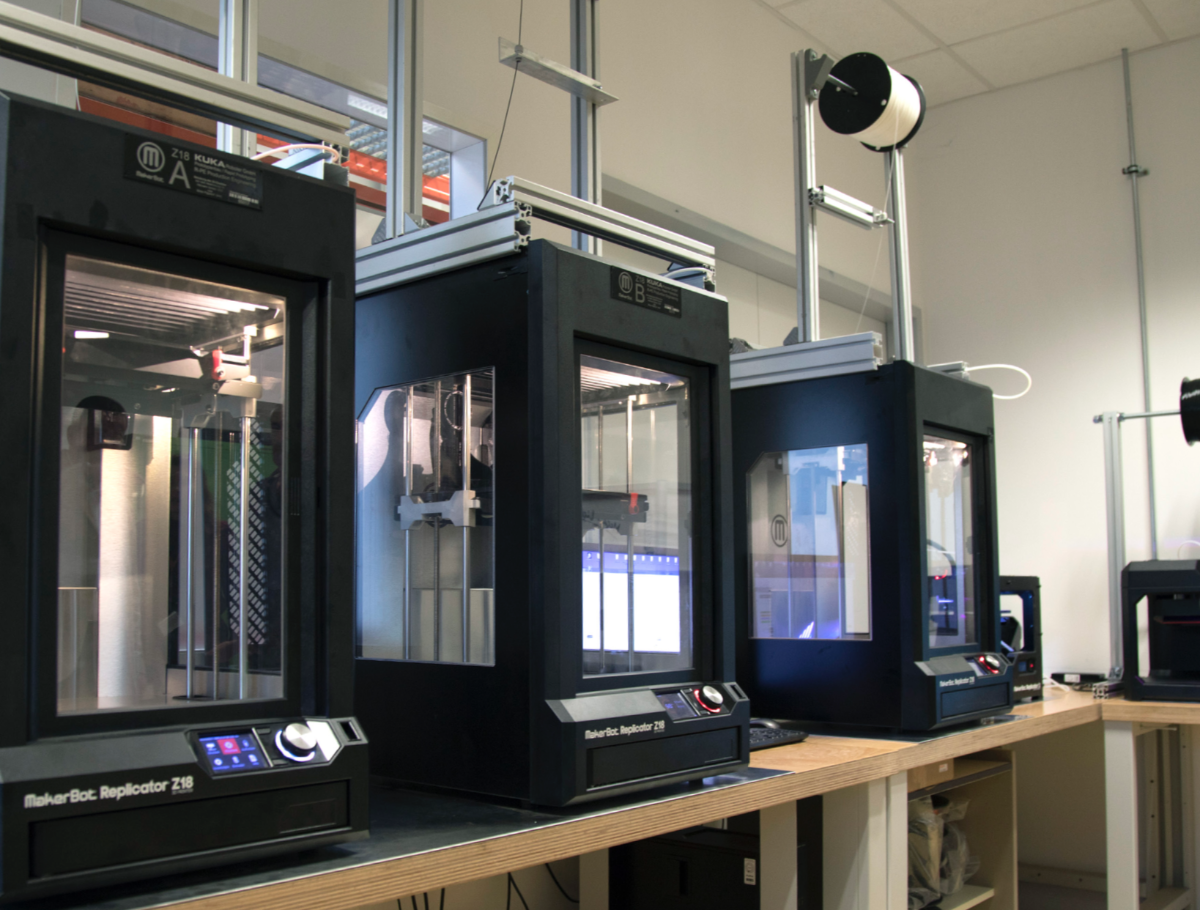
この記事は海外CBS Interactive発の記事を朝日インタラクティブが日本向けに編集したものです。